
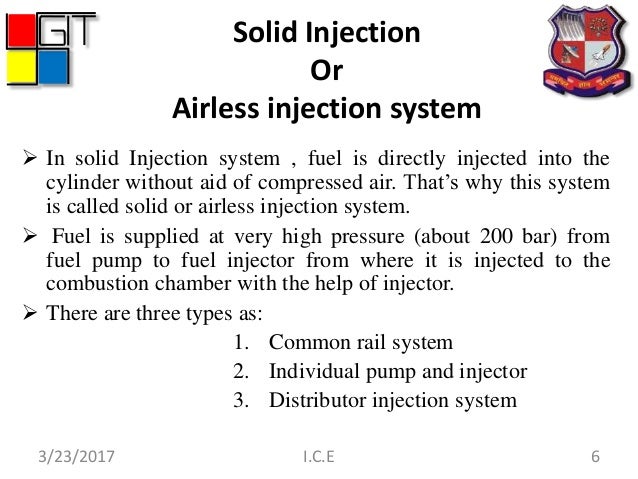
However, it would still take 2-3 decades before regulatory pressure would spur further development and the technology would mature to be commercially viable. The SOPROMI technology was evaluated by CAV Ltd. in the early 1970s and was found to provide little benefit over existing P-L-N systems in use at the time.

The CO emission is 94.5% less in the injected engine compared to the carbureted engine at 3500 rpm.Considerable work was still required to improve the precision and capability of solenoid actuators.įurther development of diesel common rail systems began in earnest in the 1980s. There is 79.3% reduction in the unburnt hydrocarbon with electronic fuel injection at 3500 rpm. The maximum brake thermal efficiency of the direct injection engine is 9.1% more than the carbureted engine at 3500 rpm. This is due to the fact that the exhaust gases may carry a small fraction of injected fuel while scavenging. For this reason, it is important to utilize the timing of the fuel injection event to optimize the mixing process.Īny further increase in the injection advance angle of 2330 results in reduction in maximum brake thermal efficiency is 22.1% at BMEP of 3.45 bar.
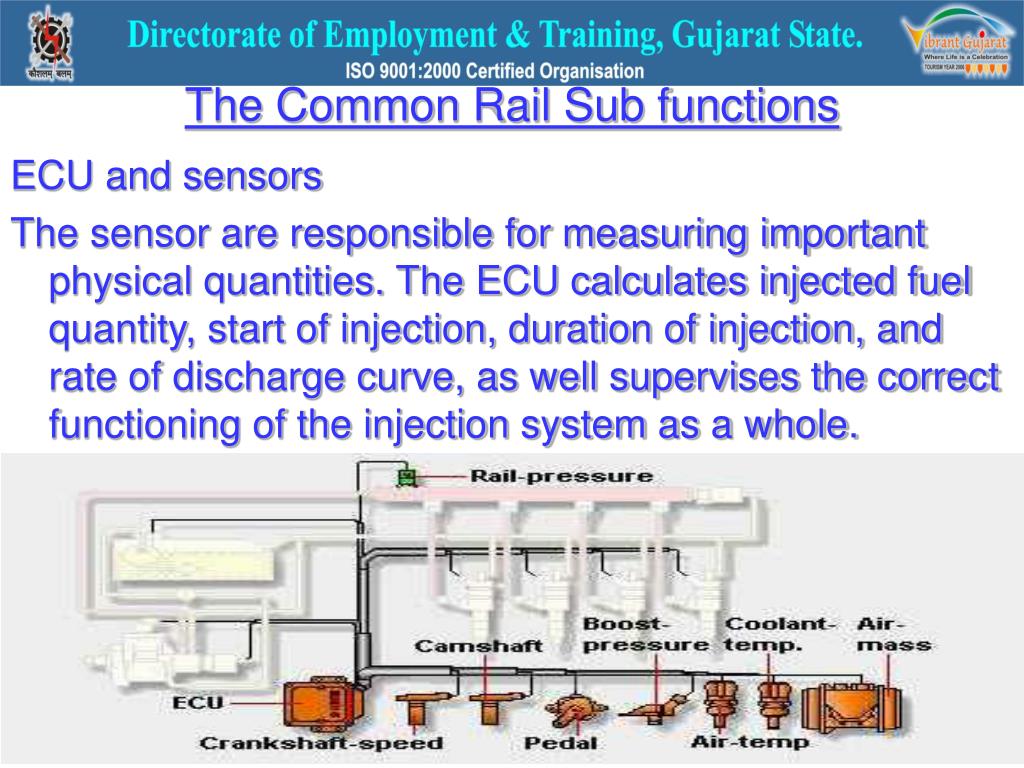
Due to the lower momentum of injected fuel, the degree of mixing in the region of the jet is lower in the gaseous case than in the liquid case. While this complexity is not present in gaseous-fueled engines since the mixing process is far from trivial. Mixture formation in a direct injected gasoline fueled engine is largely dependent on the atomization and evaporation of the fuel. It has been demonstrated, that poor mixture distribution increases the level of cycle-to-cycle combustion variability. In homogeneity in the cylinder charge creates limitations in the optimization of natural gas engines. Effect of Fuel Injection Timing on Engine Loadįuel injection timing has a strong influence on the mixing process. A water-cooled adaptor was designed for cooling the injector to prevent excess heating of the injector. Corresponding to this crank angle a hole is drilled in the cylinder bore at an inclination of 400 from horizontal. The location of the nozzle on the cylinder was determined from the pressure crank angle diagram corresponding to an in-cylinder pressure of 2 bar attained after the closure of the exhaust port. The spray would be concentrated on the upper position of the combustion chamber near the spark plug. The injection nozzle was tilted by 400 from the horizontal and injects the fuel upward, different from the method of injecting the fuel at a right angle to the cylinder axis as employed by Vieillendent, Blair, etc. The Figure shows the cylinder wall injection, with an injection nozzle installed in the cylinder wall. This requires the development of an electronically controlled direct fuel injection system fitted with suitable modification to the engine.
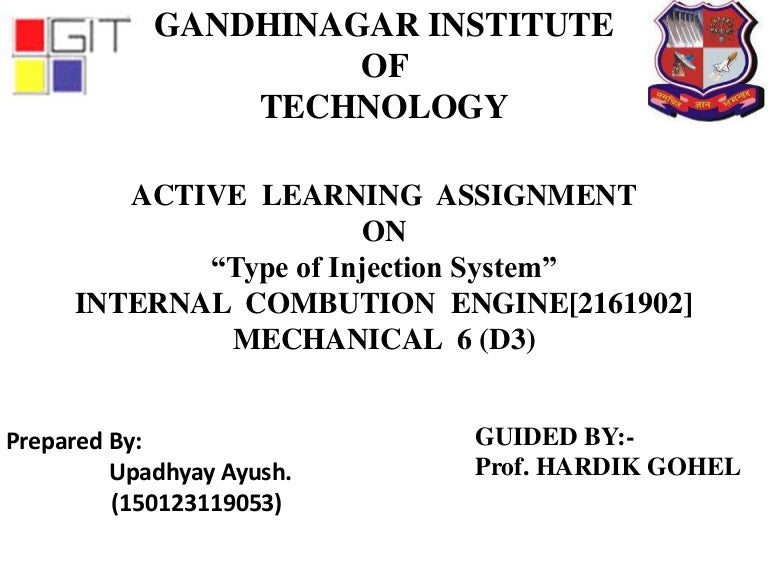
The short-circuiting losses of the two-stroke engine can be eliminated by directly injecting the fuel into the cylinder after the closure of the exhaust port.
